Your competitive advantage
Abas ERP Production highlights
Is production the source of your value creation? Then you've come to the right place, because our heart beats for production. Check out the highlights and decide for yourself.
-
All the fundamentals
For one-off, repetitive, project, contract, or subcontracting manufacturers -
Production planning
Planning methods and simulation meet your requirements -
Production control
Quick reactions thanks to full control and essential information at a glance -
Advanced Planning and Scheduling (APS)
Production control center for a high degree of automation -
CAD integration
Network your production and construction into a single team -
Revaluation
The right calculations through costing and valuation
Insight into Abas ERP
Discover Abas ERP Production
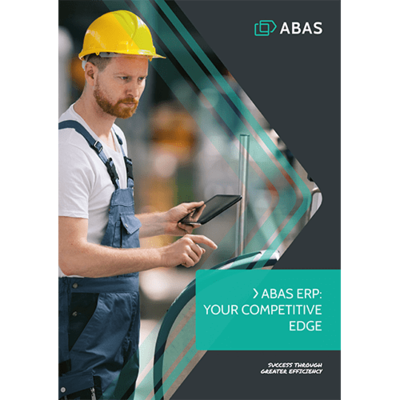
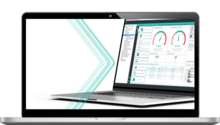
Demo Videos
Experience how Abas ERP simplifies daily tasks in production in short product videos.
Product brochure
Get to know Abas ERP and find out what makes our solution so unique.
Abas ERP Production
Abas ERP Production: Highlights in detail
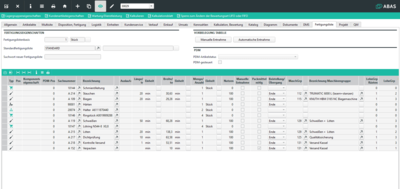
All the fundamentals for efficient production
Abas ERP has everything you need to set your production up for success. The master files are the foundation. Instead of separate BOMs and work plans, you use a combination of both in the form of production process-related production lists that contain all data such as material, operations, machines, and times in one place. Thanks to our Data Import Toolkit, you can transfer your existing master files into Abas ERP in their entirety, on your own.
Production planning - tailored to your requirements
Do you produce for stock, map different variants, or manufacture customer-specific on a project or order basis? Abas ERP offers a wide variety of planning methods tailored to your needs. These provide the flexibility you need to manufacture your various product categories. The integration of subcontract manufacturing or extended workbench as well as the consideration of optimal batch sizes or follow-up and discontinued parts control are also an integral part of Abas production planning.

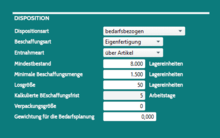
Production control with 100% transparency
Regardless of whether you want to run scheduling once a day or continuosly - thanks to our functions such as Production center or Production dashboard, you have all key information at a glance. Which work order suggestions are waiting for approval? Where are there material or resource bottlenecks? How much of a work order has already been produced and how much is still outstanding? Which customer orders are critical? Does something have to be rescheduled? You will find answers to all your questions and can intervene and take control at any time.
Master complexity with Advanced Planning and Scheduling
While rough planning automatically runs in the background, you can also perform detailed planning based on the results to narrow in a on a specific area with our fully integrated APS. With Production Planning and Control (PPC), you can stay on top of your many simultaneously running work orders, visualize production utilization, identify bottlenecks, and optimize sequencing according to diverse criteria. Do you want to serve an important customer on short notice? You can simulate this, evaluate the effects on other orders and, if the result is satisfactory, transfer the optimized detailed plan to production.
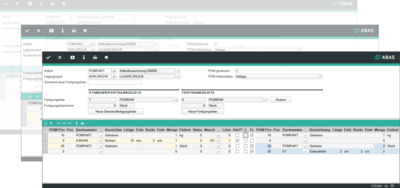
CAD integration as a link to your design team
With our CAD integration, we “translate” the dialects - design and ERP - and bring the two worlds together. While the design department benefits from direct access to ERP data, such as raw materials, assemblies, or stocks, other departments gain insight into design data or drawings. Converting design BOMs into structures suitable for production, including versioning, increases your efficiency. Even without a PDM system, you can link to products in the standard Abas ERP release. Manual data transfers and error sources as well as excessive coordination efforts are a thing of the past.
Abas ERP Production optimizes your entire production process - from planning and simulation to control.
Take advantage of knowledge gained through revaluation
Can you identify the deviations between your production planning and the times and costs actually required? Is it difficult to draw the right conclusions? Thanks to our preliminary, concurrent and followup valuation, you can get all the information you need with just a few clicks. Our valuation and material cost posting features provide important details right down to the process level. On this basis, you can incorporate the knowledge you have gained from past work orders into future work orders and gradually increase the quality of your master files.
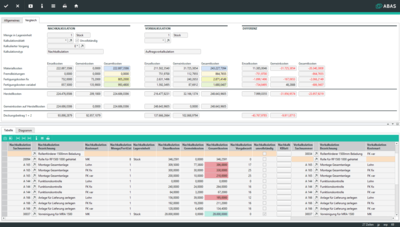
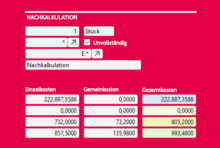
All function areas at a glance
Abas ERP supports you in all core areas of your company
Scheduling – The Abas brain
Your company has to monitor and control an enormous number of parallel processes on a daily basis. Abas ERP scheduling makes this complexity manageable. Fully automated, it permanently updates your material requirements and planning.
Production – Abas' strength
Production is the linchpin of Abas ERP. Our ERP solution helps you successfully tackle all challenges in the production environment - from production planning and execution to production control.
Financial accounting – Integrated
Benefit from the complete integration of finance in Abas ERP: From financial and fixed asset accounting, controlling, costing, and valuation to material costs posting and reporting. Always stay on top of you costs.
Customization
Thanks to our high adaptability with simultaneous upgrade compatibility, you can rely on standard software and still remain unique. Quickly and easily map your individual business processes and secure competitive advantages.
Sales – Your customer in focus
Abas ERP supports you throughout the entire sales process - starting with the sales opportunity, the efficient preparation of quotes, and order management and continuing through recording packing slips and invoices to mobile features for your external sales force.
Purchasing – Greater deadline adherence
With Abas ERP Purchasing, you can efficiently control all purchasing processes - from requests and order suggestions to incoming goods with quality control and invoice verification. With the help of the scheduling integration, you can ensure quantities and deadlines are met.
Connectivity – Made easy
Networking and interfaces are more important than ever before. Abas ERP contains powerful standard connectors (DMS, MS SQL and PDM) and, thanks to its integration tool, enables the easy connection of third-party systems without any programming effort.
Mobile applications – Anytime
Our mobile applications are intuitive to use and focus your employees on the essentials: They support your production and warehouse in real time and are also available offline for your external sales force and customer service teams.
Warehouse – Manage in Abas ERP
With the help of Abas ERP Warehouse Management, you can manage all processes relating to your material movements directly in the ERP system - from withdrawals and receipts to transfers - and easily keep an eye on stocks and delivery availability.
Abas ERP References
These customers trust in Abas ERP Production
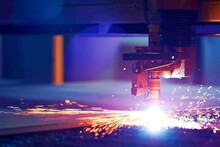
Our current ERP system tells me exactly where I am in each area. The added value at our Achern, Germany location has increased significantly. For example, we had outsourced parts of production to Slovakia and the Czech Republic. Thanks to the reorganization, we can now produce the parts more cost efficiently in Achern. As a consequence, we have brought the outsourced processes back to Achern.